Claim Your Offer
Unlock an exclusive deal at www.statisticsassignmenthelp.com with our Spring Semester Offer! Get 10% off on all statistics assignments and enjoy expert assistance at an affordable price. Our skilled team is here to provide top-quality solutions, ensuring you excel in your statistics assignments without breaking the bank. Use Offer Code: SPRINGSAH10 at checkout and grab this limited-time discount. Don’t miss the chance to save while securing the best help for your statistics assignments. Order now and make this semester a success!
We Accept
- Understanding Control Charts
- 1. Collecting Data
- 2. Calculating Control Limits
- 3. Plotting Control Charts
- Estimating Process Mean and Standard Deviation
- 1. Process Mean
- 2. Process Standard Deviation
- Assessing Process Capability
- 1. Capability Indices
- 2. Interpreting Results
- Determining Process Control
- 1. Analyzing Control Charts
- 2. Identifying Patterns
- Solving Assignments Using Minitab
- 1. Inputting Data
- 2. Generating Control Charts
- 3. Calculating Statistics
- 4. Performing Capability Analysis
- 5. Interpreting and Reporting Results
- Example: Six Sigma Analysis
- 1. Defining Specifications
- 2. Calculating Current Sigma Level
- 3. Determining Variability Reduction
- Conclusion
When solving Minitab assignments that involve control charts, process mean and standard deviation estimation, process capability assessment, and process control determination, having a structured approach is crucial. These assignments often require the use of software like Minitab to perform calculations and interpret results effectively. In this blog, we'll guide you through the key steps to excel in these types of statistics assignments, ensuring you can confidently tackle similar problems in the future.
Understanding Control Charts
Control charts are essential tools in quality control and process management. They help monitor the stability and performance of a process over time. There are different types of control charts, including X-bar, R, and S charts, each serving a specific purpose. Here’s how to approach setting up and interpreting these charts.
1. Collecting Data
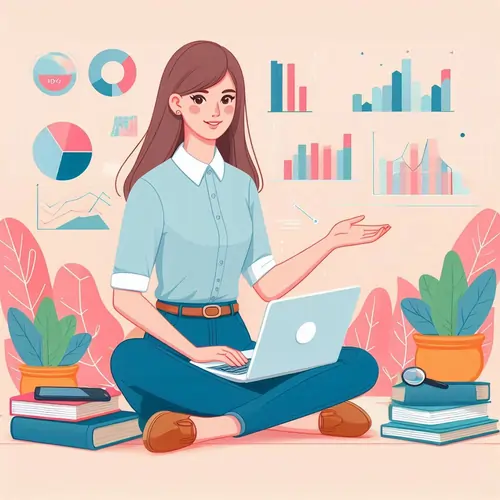
The first step in any control chart analysis is data collection. This involves gathering preliminary subgroups of data. For instance, if you have 25 subgroups each consisting of 3 measurements, you will collect a total of 75 data points. Ensure that your data collection process is consistent and accurate to avoid errors in your analysis.
2. Calculating Control Limits
Once you have your data, the next step is to calculate control limits. Control limits are the thresholds that determine whether a process is in control or out of control.
For an X-bar chart, you need to calculate the average of the subgroup means. For an R chart, you calculate the range (the difference between the highest and lowest values) of each subgroup. These averages are then used to determine the control limits using specific statistical formulas or directly through Minitab.
3. Plotting Control Charts
In Minitab, you can easily plot control charts by navigating to the appropriate menu options. For example, to create an X-bar chart, you would go to Stat > Control Charts > X-bar Chart. Enter your data into Minitab’s worksheet, and the software will generate the control chart along with the calculated control limits. This visual representation helps in identifying any points that fall outside the control limits, indicating potential issues in the process.
Estimating Process Mean and Standard Deviation
Estimating the process mean and standard deviation is crucial for understanding the central tendency and variability of your process. Here’s how to do it:
1. Process Mean
The process mean is the average value of your data points. In control chart analysis, you calculate the process mean by averaging the subgroup means. This gives you an idea of where the center of your data lies.
2. Process Standard Deviation
The process standard deviation measures the spread or dispersion of your data. It can be estimated using the average range of the subgroups and a specific statistical factor obtained from standard tables. Minitab simplifies this process by providing built-in functions to calculate the standard deviation based on your data.
Assessing Process Capability
Process capability analysis evaluates how well your process can produce output within specified limits. This is a key aspect of quality control, as it helps determine whether your process meets customer requirements.
1. Capability Indices
To assess process capability, you use indices like Cp, Cpk, Pp, and Ppk. These indices compare the spread of your process data to the specification limits. Higher values indicate a more capable process.
In Minitab, you can perform capability analysis by navigating to Stat > Quality Tools > Capability Analysis. Enter your specification limits and data, and Minitab will calculate the capability indices for you. The results will help you understand whether your process is capable of consistently producing output within the desired specifications.
2. Interpreting Results
Interpreting the results of a capability analysis involves comparing the calculated indices to industry benchmarks. For instance, a Cp or Cpk value of 1.33 or higher typically indicates a capable process. If your indices are lower, it suggests that the process variability is too high, and improvements are needed.
Determining Process Control
Determining whether a process is in statistical control is essential for maintaining quality. Here’s how to assess process control:
1. Analyzing Control Charts
The primary tool for determining process control is the control chart. By analyzing the control charts, you can identify points that fall outside the control limits. These points indicate potential issues that need to be addressed.
2. Identifying Patterns
In addition to looking for points outside the control limits, you should also identify patterns in the data. Non-random patterns such as trends, cycles, or shifts can indicate that the process is not in control. Recognizing these patterns helps in diagnosing and correcting process issues.
Solving Assignments Using Minitab
Using Minitab for solving control chart and process capability assignments can significantly streamline your work. Here’s a typical approach to tackling these assignments using Minitab:
1. Inputting Data
Start by entering your data into Minitab’s worksheet. Ensure that your data is organized correctly, with each column representing a different subgroup or measurement.
2. Generating Control Charts
Follow the steps outlined earlier to create the appropriate control charts. For example, to create an X-bar and R chart, go to Stat > Control Charts > X-bar and R Chart. Enter your data, and Minitab will generate the charts along with the control limits.
3. Calculating Statistics
Use Minitab’s built-in functions to calculate the necessary statistics, such as process mean and standard deviation. Navigate to Stat > Basic Statistics and choose the relevant options to perform these calculations.
4. Performing Capability Analysis
Conduct a capability analysis by going to Stat > Quality Tools > Capability Analysis. Enter your data and specification limits, and Minitab will calculate the capability indices and generate a capability report.
5. Interpreting and Reporting Results
Finally, interpret the results generated by Minitab. Look at the control charts to assess process control and analyze the capability indices to determine process capability. Prepare a report summarizing your findings, including any recommendations for process improvements.
Example: Six Sigma Analysis
Achieving Six Sigma quality requires a deep understanding of process variability and capability. Here’s how to approach a Six Sigma analysis using Minitab:
1. Defining Specifications
Start by defining your specifications. For instance, if the specifications are 2.25 ± 4, enter these limits into Minitab during the capability analysis.
2. Calculating Current Sigma Level
Use Minitab to calculate the current sigma level of your process. This involves comparing your process performance to Six Sigma standards, which aim for 3.4 defects per million opportunities.
3. Determining Variability Reduction
Assess the needed reduction in process variability to achieve Six Sigma quality. Minitab’s capability analysis tools can help you determine the extent of variability reduction required.
Conclusion
By following these steps and utilizing Minitab effectively, you can confidently approach and complete your statistics assignment involving control charts and process capability analysis. This structured approach ensures you understand the essential concepts and can apply them practically, leading to success in your statistics assignments. Remember, the key to mastering these assignments is practice and familiarity with the tools and techniques discussed in this guide. With consistent effort and the right resources, you'll be well-equipped to ace your control chart assignments in statistics.