Claim Your Offer
Unlock an exclusive deal at www.statisticsassignmenthelp.com with our Spring Semester Offer! Get 10% off on all statistics assignments and enjoy expert assistance at an affordable price. Our skilled team is here to provide top-quality solutions, ensuring you excel in your statistics assignments without breaking the bank. Use Offer Code: SPRINGSAH10 at checkout and grab this limited-time discount. Don’t miss the chance to save while securing the best help for your statistics assignments. Order now and make this semester a success!
We Accept
- Understanding the Basics of Control Charts
- Steps to Set Up Control Charts
- Example Calculation
- Estimating Process Mean and Standard Deviation
- Assessing Process Capability
- Addressing Specific Assignment Tasks
- Setting Up Control Charts
- Estimating Process Parameters
- Process Capability Analysis
- Using Software Tools
- Conclusion
Quality control plays a crucial role in ensuring that manufacturing and production processes meet the necessary standards and specifications. For students studying statistics, mastering the application of quality control methods is essential, particularly when tasked with assignments involving control charts and process capability analysis. This comprehensive guide is designed to assist students in effectively solving statistics assignments related to assistance with your quality control assignment.
Understanding the basics of control charts is fundamental. These tools monitor process stability and variability over time, providing visual insights into trends and anomalies. By following structured steps to set up control charts, calculate control limits, and estimate process parameters such as mean and standard deviation, students can gain proficiency. Software tools like Minitab facilitate these calculations and analyses, enhancing both learning and practical application.
Understanding the Basics of Control Charts
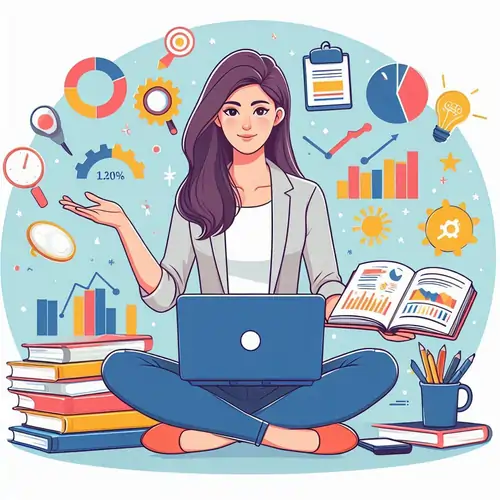
Control charts are invaluable tools used in statistical process control to monitor the stability and variability of a process over time. They provide visual representations of process data, helping to identify trends, shifts, or anomalies that may indicate process issues. Several types of control charts exist, each serving a specific purpose depending on the nature of the data and sample size.
X-bar and R charts are typically used when the sample size is small, providing insights into the process mean and range. On the other hand, X-bar and S charts are preferred for larger sample sizes, offering a view of process standard deviation. Individual/moving range charts are useful when data are collected one at a time or in small groups.
By plotting data points and setting control limits based on statistical calculations, control charts enable practitioners to distinguish between common cause variation and special cause variation, guiding decisions for process improvement and quality assurance.
Steps to Set Up Control Charts
Setting up control charts involves several crucial steps that ensure the accurate monitoring and assessment of process stability and variability.
- Collect Data:To begin setting up control charts, gather a sufficient number of samples from the process under observation. For example, if you have data for 25 subgroups, each with three observations, record the means (X-bar) and standard deviations (S) for each subgroup. This step is crucial as it forms the basis for calculating control limits.
- Calculate Control Limits: After collecting the data, the next step is to compute control limits. Control limits are boundaries that represent the expected range of variation in the process. These limits are calculated using statistical formulas and control chart constants that are specific to the sample size and the type of control chart being used. For instance, X-bar and R charts have different formulas for calculating control limits compared to X-bar and S charts.
By following these steps meticulously, you can ensure that your control charts accurately reflect the variability of the process and are capable of detecting any shifts or trends that may occur.
Example Calculation
Suppose we're given:
- Sum of subgroup means (X-bar) = 55.45
- Sum of subgroup standard deviations (S) = 28.67
- Number of subgroups = 25
- Sample size = 3
We can then calculate the averages of X-bar and S. With control chart constants, we derive the Upper Control Limit (UCL) and Lower Control Limit (LCL) for both X-bar and S charts.
Estimating Process Mean and Standard Deviation
Once control charts are established and the process is deemed in control, estimating the process mean and standard deviation becomes crucial for further analysis. The process mean, representing the central tendency of the process, is simply the average of X-bar values obtained from the control charts. This mean is a key indicator of the process's performance over time.
Similarly, the process standard deviation, which measures the variability or dispersion of the process data, is calculated using the average of S values along with a control chart constant. This constant depends on the subgroup size and is essential for determining the Upper Control Limit (UCL) and Lower Control Limit (LCL) of the control charts.
Estimating these parameters accurately is vital for understanding the process's capability and ensuring it meets predefined quality standards. It allows for effective decision-making and continuous improvement efforts aimed at enhancing process efficiency and product quality.
Assessing Process Capability
To determine if a process meets specifications, various process capability indices are calculated, such as Cp, Cpk, and the percentage of nonconforming parts. These indices provide insights into the process's ability to meet customer requirements effectively. Cp measures the potential capability of a process to produce within specification limits, whereas Cpk considers both process centering and spread. These indices are computed using the process standard deviation and specification limits. Additionally, the percentage of nonconforming parts is determined by assessing the proportion of items produced outside the specification limits. These calculations are crucial for evaluating the robustness and efficiency of the manufacturing or production process. By using statistical tools and methods, engineers and quality professionals can ensure that products consistently meet quality standards, thereby enhancing customer satisfaction and reducing the risk of defects or failures in the field.
Addressing Specific Assignment Tasks
When tackling quality control assignments, several specific tasks must be addressed to ensure a thorough understanding and application of statistical methods.
Setting Up Control Charts
The first task involves setting up control charts, such as X-bar and S charts or X-bar and R charts, depending on the nature of the data and sample size. Control charts help monitor process stability and identify any changes or trends that may indicate process issues. By plotting subgroup means (X-bar) and subgroup ranges (R or S), students can visually assess whether the process is within control limits.
Estimating Process Parameters
After setting up control charts and confirming that the process is stable, the next step is to estimate process parameters. This includes calculating the process mean and standard deviation. The process mean (X-bar) is calculated from the averages of the subgroup means, while the process standard deviation (S or R-bar) is calculated using the average of the subgroup standard deviations. These parameters provide insights into the central tendency and variability of the process.
Process Capability Analysis
To determine if the process meets specifications, various process capability indices are calculated, such as Cp, Cpk, and the percentage of nonconforming parts. Cp measures the potential capability of a process to produce within specification limits, while Cpk assesses both process centering and spread. The percentage of nonconforming parts indicates how many products fall outside the specification limits. These calculations help evaluate whether the process is capable of consistently meeting customer requirements.
Using Software Tools
Software tools like Minitab are invaluable for conducting these analyses efficiently. Minitab automates statistical calculations, charts, and reports, allowing users to input data, select the appropriate control charts, and interpret results accurately. This software simplifies complex statistical processes and enhances decision-making by providing clear, actionable insights.
Conclusion
Mastering quality control assignments requires a solid grasp of control chart principles, process capability analysis, and statistical techniques. Students can approach these assignments with confidence by following the systematic steps outlined in this guide. By understanding how to set up and interpret control charts, estimate process parameters, and assess process capability, they gain essential skills applicable across various industries. These assignments provide practical experience in using tools like Minitab for data analysis and interpretation. Through consistent practice and application, students not only enhance their statistical proficiency but also prepare themselves for real-world challenges in quality management. For personalized guidance and support, services such as StatisticsAssignmentHelp.com offer expert assistance to ensure students excel in their coursework and develop a deep understanding of quality control principles. With dedication and a thorough understanding of these methodologies, students can effectively solve statistics assignments and contribute to improving processes in their future careers.