Claim Your Offer
Unlock an exclusive deal at www.statisticsassignmenthelp.com with our Spring Semester Offer! Get 10% off on all statistics assignments and enjoy expert assistance at an affordable price. Our skilled team is here to provide top-quality solutions, ensuring you excel in your statistics assignments without breaking the bank. Use Offer Code: SPRINGSAH10 at checkout and grab this limited-time discount. Don’t miss the chance to save while securing the best help for your statistics assignments. Order now and make this semester a success!
We Accept
In today's highly competitive market, ensuring the highest level of quality in manufacturing processes is paramount to success. Quality control, which is essential to complete your Six Sigma Assignment, serves as the cornerstone of manufacturing operations. Among the various methodologies employed to achieve this, Six Sigma stands out as a powerful approach that has revolutionized the way organizations manage quality and operational efficiency.
Quality Control in Manufacturing
Quality control in manufacturing is a comprehensive system of processes, techniques, and strategies designed to ensure that products meet predefined standards of quality, performance, and reliability. It encompasses every aspect of production, from raw material inspection to the final product evaluation. The primary objective is to identify and eliminate defects, deviations, and variations that could compromise the end product's quality.
Quality control is an integral part of manufacturing processes that ensures products meet or exceed predetermined standards of quality, performance, and reliability. It encompasses a series of systematic steps aimed at identifying, addressing, and preventing defects, variations, and inefficiencies. Let's delve into the key steps involved in the process of quality control:
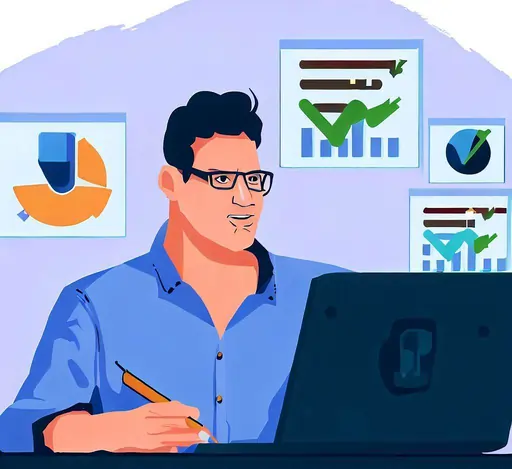
- Quality Planning
Quality planning lays the foundation for the entire quality control process. During this phase, organizations define the quality standards, specifications, and requirements that products must meet. This step is crucial in establishing a clear understanding of what constitutes an acceptable product. Key activities within quality planning include:
- Defining Quality Standards: Determine the specific characteristics, features, and attributes that define a high-quality product. These standards could encompass physical, functional, and performance attributes.
- Setting Specifications: Establish measurable specifications for various aspects of the product, such as dimensions, tolerances, materials, and safety features.
- Identifying Quality Control Measures: Determine the methods and techniques that will be employed to monitor and evaluate product quality throughout the manufacturing process.
- Designing Quality Tests: Develop a plan for conducting tests, inspections, and evaluations to verify that the product meets the established quality standards.
Quality assurance focuses on ensuring that the planned quality standards are achieved consistently throughout the manufacturing process. This phase involves implementing systematic processes and procedures to prevent defects and non-conformities from arising. Key activities in quality assurance include:
- Process Documentation: Create detailed documentation of manufacturing processes, including procedures, work instructions, and quality control checkpoints.
- Training and Education: Provide training to employees involved in the manufacturing process to ensure they understand the quality standards and their roles in maintaining them.
- Preventive Measures: Implement measures to prevent defects from occurring in the first place. This can involve using preventive maintenance, standardized operating procedures, and thorough inspections.
- Quality Audits: Conduct regular audits to assess whether the implemented processes are in compliance with established quality standards and identify areas for improvement.
Quality control is the phase where products are actively tested, measured, and evaluated against predefined quality standards. This step involves the hands-on assessment of the product to identify any defects or variations that may have occurred during the manufacturing process. Key activities in quality control include:
- Inspection: Physically examine the product to identify any visual defects, deviations from specifications, or irregularities.
- Testing: Conduct various tests to assess the product's performance, functionality, and durability. These tests may include stress testing, functional testing, and reliability testing.
- Data Analysis: Analyze data collected during inspections and tests to identify trends, patterns, and anomalies. Statistical analysis tools can be employed to make informed decisions.
- Acceptance or Rejection: Determine whether the product meets the predefined quality standards. Products that pass the quality control measures are accepted, while those that fail are rejected or subjected to corrective action.
Continuous improvement is an ongoing and iterative process that is woven into the fabric of quality control. It involves analyzing data, identifying areas for enhancement, and implementing corrective actions to prevent future defects. Key activities within continuous improvement include:
- Data Analysis: Analyze the data collected during quality control processes to identify patterns, trends, and areas of concern.
- Root Cause Analysis: Identify the underlying causes of defects or variations. This helps to address the core issues rather than just treating the symptoms.
- Implement Corrective Actions: Develop and implement strategies to address the identified issues and prevent similar defects from occurring in the future.
- Feedback Loop: Incorporate lessons learned and insights gained from continuous improvement efforts back into the quality planning and assurance stages. This ensures a feedback loop that drives ongoing enhancement.
Introduction to Six Sigma
Six Sigma is a data-driven, systematic methodology for process improvement that aims to eliminate defects and minimize variations in manufacturing and other business processes. Developed by Motorola in the 1980s and popularized by companies like General Electric, Six Sigma focuses on achieving near-perfect performance by reducing the occurrence of defects to a statistically minimal level—approximately 3.4 defects per million opportunities.
The term "Six Sigma" comes from the statistical concept of standard deviations (σ), where a Six Sigma process represents a highly controlled and consistent process with minimal variability. The methodology incorporates two main methodologies: DMAIC (Define, Measure, Analyze, Improve, Control) and DMADV (Define, Measure, Analyze, Design, Verify).
The DMAIC Process in Six Sigma
- Define: In this phase, the project goals, scope, and deliverables are defined. The primary focus is on understanding the problem and its impact on the business.
- Measure: In this step, data is collected to quantify the current state of the process. Key performance indicators (KPIs) are established, and the process is assessed for its baseline performance.
- Analyze: Data is analyzed to identify root causes of defects and variations. Tools such as cause-and-effect diagrams and Pareto charts are used to pinpoint the most critical factors affecting quality.
- Improve: Based on the analysis, potential solutions are developed and implemented. The goal is to optimize the process and eliminate identified root causes of defects.
- Control: Once improvements are made, control measures are established to ensure the sustained performance of the process. Monitoring, ongoing measurement, and adjustments are performed to prevent backsliding into previous states of poor quality.
Implementing Six Sigma in manufacturing offers a range of benefits that contribute to enhanced quality control and overall business success:
- Reduced Defects: By minimizing variations and defects, Six Sigma helps reduce the likelihood of product recalls, warranty claims, and customer complaints, resulting in higher customer satisfaction.
- Increased Efficiency: Through process optimization, Six Sigma eliminates waste, reduces cycle times, and enhances overall operational efficiency.
- Data-Driven Decisions: Six Sigma relies on data analysis and statistical tools, ensuring that decisions are based on accurate information rather than intuition.
- Cultural Shift:Six Sigma promotes a culture of continuous improvement and empowers employees at all levels to participate in quality enhancement initiatives.
- Cost Savings: Improved efficiency and reduced defects lead to significant cost savings in terms of materials, labor, and rework.
Challenges in Implementing Six Sigma
The implementation of Six Sigma, despite its potential for substantial benefits, is not without its challenges. Organizations embarking on a Six Sigma journey must be prepared to navigate these obstacles to ensure a successful and effective deployment of the methodology. Let's delve deeper into the challenges associated with implementing Six Sigma:
- Cultural Resistance
Transitioning from traditional methods to a data-driven, systematic approach like Six Sigma can encounter significant resistance from employees who are accustomed to established practices. This resistance is often rooted in a fear of change, the perception that Six Sigma is an additional burden, and concerns about job security. Overcoming cultural resistance requires:
- Effective Communication: Clear communication about the benefits of Six Sigma and how it aligns with the organization's goals can alleviate apprehensions and foster buy-in.
- Employee Involvement: Involving employees in the implementation process, seeking their input, and addressing their concerns can create a sense of ownership and commitment.
- Leadership Support: Strong endorsement and support from top leadership can influence employees to embrace the new methodology.
Implementing Six Sigma requires significant investments in terms of time, money, and human resources. These investments are essential to provide the necessary infrastructure for successful implementation. Organizations need to allocate resources for:
- Training: Employees need to be trained in Six Sigma methodologies, statistical tools, and data analysis techniques. This training ensures that team members can effectively contribute to improvement projects.
- Technology: Implementing Six Sigma often involves using specialized software and tools for data collection, analysis, and process optimization.
- Dedicated Personnel: Organizations may need to assign dedicated personnel or teams to lead and manage Six Sigma projects. These individuals drive the implementation and ensure its success.
Six Sigma methodologies and statistical tools can be complex, especially for employees who are new to the approach. The technical nature of Six Sigma can lead to challenges in understanding, applying, and interpreting the methodologies. To address this complexity:
- Thorough Training: Comprehensive training programs are crucial to equip employees with the necessary skills and knowledge to effectively implement Six Sigma tools.
- Guidance and Support: Providing access to experts or mentors who have experience with Six Sigma can help employees navigate challenges and gain a better understanding of the methodologies.
Introducing Six Sigma into an organization is a significant endeavor that often requires fundamental changes to established processes and workflows. However, the disruption caused by such changes can lead to resistance and pushback from employees who are comfortable with the existing way of doing things. Effective change management strategies are crucial to ensuring a smooth and successful transition to the Six Sigma methodology. Here's how organizations can navigate the challenges associated with change management during Six Sigma implementation:
- Communicate a Clear Vision
Communication is key to overcoming resistance to change. Employees are more likely to embrace change when they understand its purpose and how it aligns with the organization's goals. To facilitate this understanding, leaders should:
- Clearly Articulate the Vision: Clearly communicate the reasons for introducing Six Sigma and the benefits it can bring to the organization, such as improved quality, increased efficiency, and enhanced competitiveness.
- Connect to Organizational Goals: Explain how Six Sigma supports the organization's overall strategic objectives and how it can contribute to the success of the company.
- Address Concerns: Anticipate and address potential concerns or misconceptions that employees might have. This demonstrates that their input and feelings are valued.
Sudden and drastic changes can lead to resistance and confusion among employees. A gradual implementation approach allows teams to adapt to new processes over time, mitigating the shock of abrupt changes. Steps to consider include:
- Pilot Projects: Begin with small-scale Six Sigma pilot projects in specific areas of the organization. This approach allows teams to learn and adapt to the new methodologies without disrupting the entire organization.
- Phased Rollout: Gradually expand Six Sigma initiatives to different departments or units, allowing teams to learn from each other's experiences and successes.
- Training and Support: Provide adequate training and support throughout the implementation process to ensure that employees have the necessary skills and knowledge to adopt new practices.
Incorporating feedback from employees during the change process is vital for identifying challenges and areas that require adjustment. Establishing feedback mechanisms encourages open communication and collaboration. Strategies for collecting and using feedback include:
- Regular Check-ins: Schedule regular meetings or sessions to allow employees to voice their concerns, share insights, and provide feedback on the implementation progress.
- Cross-Functional Teams: Form cross-functional teams that include representatives from different departments. This diversity ensures a comprehensive understanding of the challenges faced during implementation.
- Actionable Insights: Act on the feedback received by making necessary adjustments to the implementation plan. This demonstrates to employees that their input is valued and contributes to meaningful change.
Recognizing and rewarding employees for their contributions to Six Sigma initiatives can play a crucial role in motivating them to embrace change and actively participate in improvement efforts. Consider the following approaches:
- Celebrate Successes: Acknowledge and celebrate achievements and milestones reached during Six Sigma projects. This recognition reinforces the importance of the changes and the positive impact they bring.
- Incentives and Rewards: Offer incentives or rewards for employees who actively engage in Six Sigma projects, contribute innovative ideas, or demonstrate exceptional commitment to the new methodologies.
- Career Growth Opportunities: Highlight how participation in Six Sigma initiatives can lead to career growth and skill development for employees. This can encourage them to view the changes as opportunities rather than challenges.
Effective change management is pivotal in ensuring a smooth and successful transition to Six Sigma methodologies. By communicating a clear vision, implementing changes gradually, gathering employee feedback, and recognizing contributions, organizations can overcome resistance and foster a culture of continuous improvement. In doing so, they can leverage the full potential of Six Sigma to achieve higher levels of quality, efficiency, and competitiveness.
Real-World Application of Six Sigma in Manufacturing
Many companies have successfully implemented Six Sigma to achieve remarkable improvements in quality control and operational efficiency:
- General Electric (GE): One of the earliest adopters of Six Sigma, GE saved billions of dollars by reducing defects and optimizing processes across various business units.
- Motorola: The birthplace of Six Sigma, Motorola used the methodology to significantly enhance its manufacturing processes, leading to improved customer satisfaction and product quality.
- Toyota: Although known for its Lean manufacturing practices, Toyota integrated Six Sigma to further enhance quality and efficiency in its production processes.
Conclusion
Quality control in manufacturing is a critical factor in delivering products that meet or exceed customer expectations. Six Sigma, with its rigorous data-driven approach and systematic methodology, has proven to be a powerful tool for achieving exceptional quality, minimizing defects, and optimizing processes. While the implementation of Six Sigma presents challenges, the benefits it offers in terms of cost savings, efficiency improvements, and enhanced customer satisfaction make it a valuable strategy for any manufacturing organization striving for excellence in quality control.